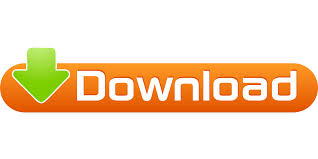
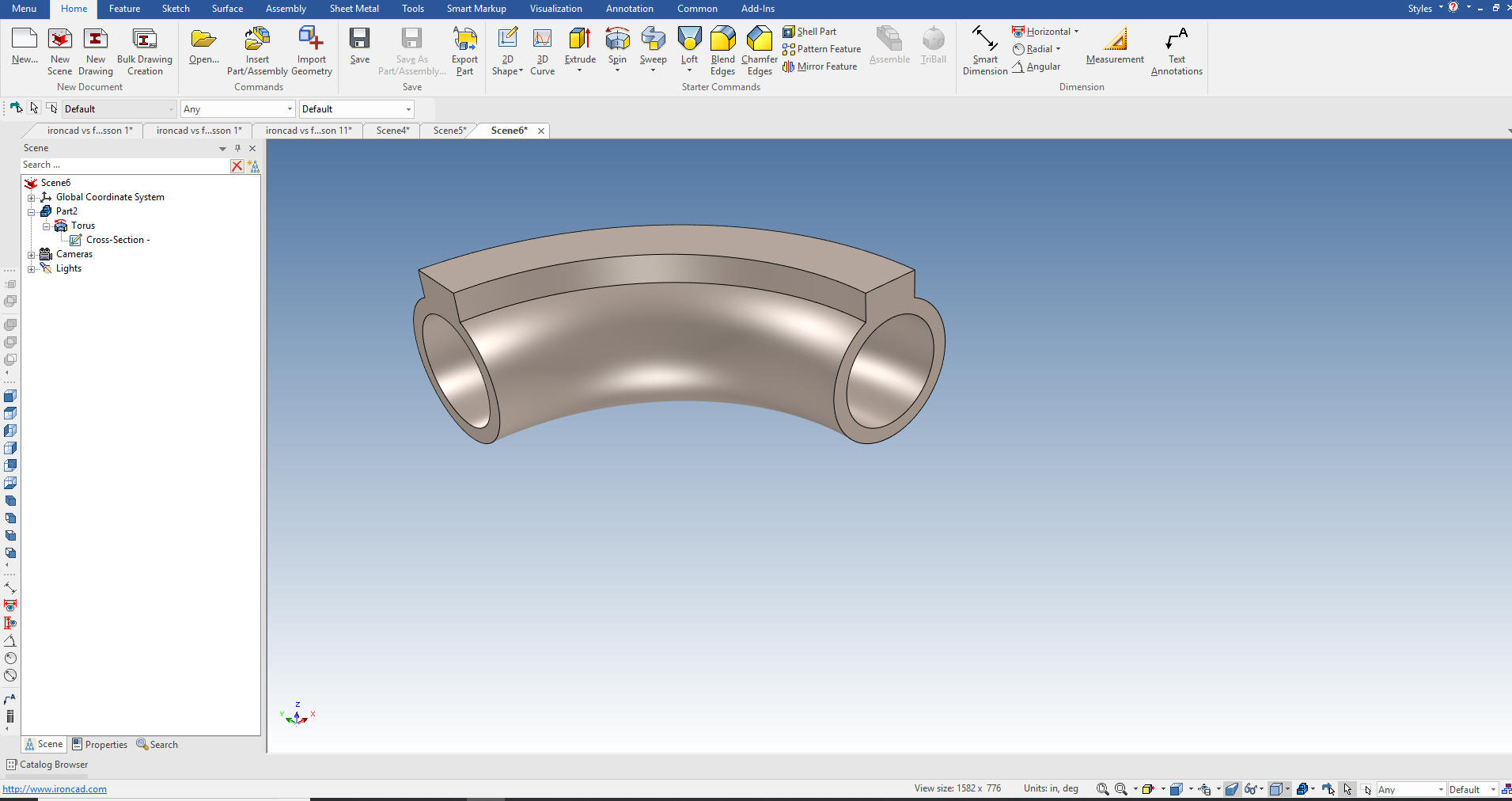
The welded sheet metal component has to be surface finished to remove the sharp edges and to optimize the cosmetic appearance of the product. The forming limit of the sheet is considered while developing the component and it varies with materials and thicknesses. This can be done by brake press machines using V-bend dies, goose-neck dies, U-bend dies, etc.ĭrawing involves readily drawing of the sheet metal blank into a forming die with the help of a mechanical punch to obtain a hollow or curved surface. A die and punch are used to shear the sheet into the required shapes.īending is a metal forming process used to bend the sheet along a straight axis. Mechanical shearing is a quicker process compared to laser cutting. Mechanical shearing: To cut the metal sheet into shapes for mass production mechanical shearing is used.

It also gives the same tolerance as Laser cutting but the surface finish varies depending on parameters. It can cut up to 150mm thick plates but the speed is less compared to Laser cutting.

When the sheet metal is put through the process of bending the metal around, the bend is deformed and stretched. The Bend Allowance is defined as the material to add to the actual leg lengths of the part to develop a flat pattern. Generic values for K Factor varies from 0.3 to 0.5. K Factor changes its value with respect to physical properties and thickness of materials.
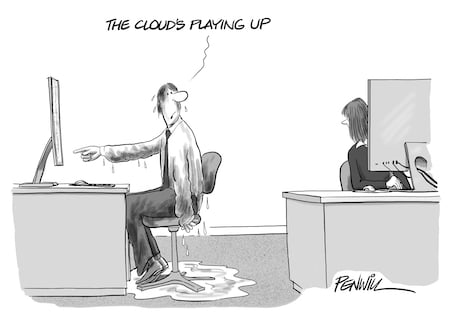
The K Factor in sheet metal working is the ratio of the neutral axis to the material thickness. Spacing between holes should be at least two times the sheet metal thickness. If the hole gets too close to an edge a bulge can appear near an edge. Holes diameter less than the sheet metal thickness results in higher punch loading, longer burnish in the holes and excessive burr. Keep holes and slots diameter at least as large as sheet metal thickness. Whenever making a bend, it is always preferred to make bends in a single plane as this will avoid any additional reorientation while manufacturing that part. The bend radii should be maintained consistently throughout the part as keeping the same bend radii across all bends makes the part cost effective. To avoid any fractures or distortions, it is necessary to keep inside bend radius at least equal to sheets thickness. Parts with different thicknesses will have different bend parameters which may result in the inaccuracy of the desired shape. Geometry with more than one wall thickness requires sheets of different thicknesses, which requires reorientation and alignment of parts that consume time. While designing any geometry, it is always a good idea to maintain uniform wall thickness throughout the body. Below are the factors designer needs to consider while modeling a sheet metal component.
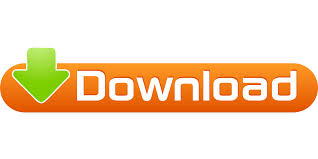